Friction Welding
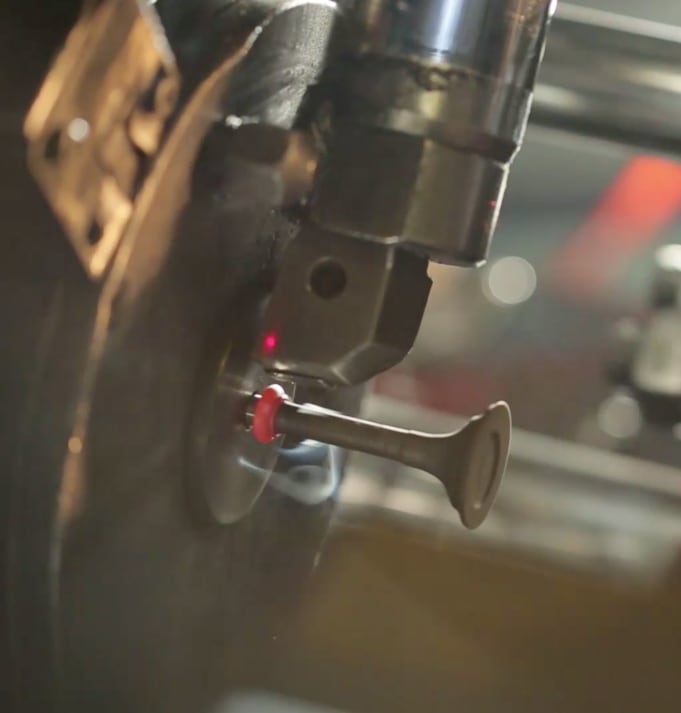
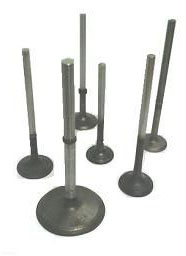
At STYM with the use of 14 state of the art Friction welding Machines we have the capability to manufacture bi-metallic Engine valves in any sizes. The process of Friction welding for us can start before or after the Die forge process depending on our customer’s need. The process before the die forging consists of the two steel alloy bars being friction welded together(bar-to-bar) thereafter it is processed for die forging and forming of the valve head. The Friction welding process after the die forging is in a way that that the head of valve is first forged then it goes through the friction welding and fuses with the stem(head-to-bar).
Also at STYM the Friction Welding process is additionally used for the hollow stem and sodium filled engine valves.
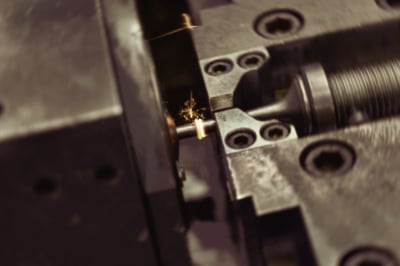
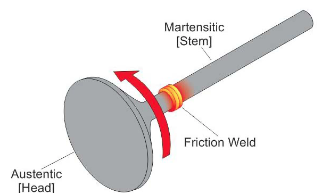
Friction welding is a process used for bi-metallic engine valves. This is a solid-state welding process which generates heat through mechanical friction between workpieces of the engine valve in relative motion to one another, and with the addition of a lateral force known as the “upset” it displaces and fuses the materials. Based on the fact that no melting occurs, friction welding is not actually a welding process in the traditional sense, but a forging technique. However, due to the similarities between this technique and traditional welding, the term has become common.
In Friction welding process for the manufacturing of engine valve workpieces, one of the workpieces has the rotary state and the other one is in the non rotary state. A pressure is applied to the non-rotary workpiece and pushed towards the rotary on, within the friction area of the two pieces the generated heat will create an upset and fuse the two workpieces together. The extra material around the friction welding interface area will be then removed in the later process.
In Bi-metallic Engine Valve manufacturing two different steel alloys are friction welded to one another. Exhaust Engine valves are the most commen application for the Friction Welding process as the head of the valve is made of Austenitic Steel, for better heat and corrosion resistance and non-magnetic properties, and the stem of the valve is made of the Martensitic Steel which has high strength , abrasive wear resistance properties and also magnetic properties.